【アジャイル経営のススメ】第6回 かんばん方式
作成日:2023.08.03 更新日:2023.08.03 公開日:2023.08.03
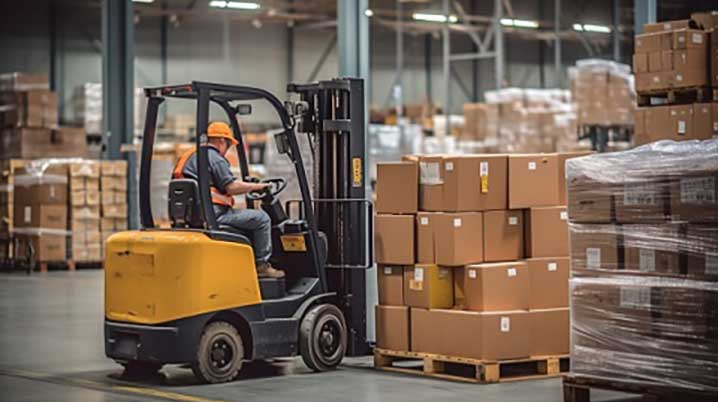
■トヨタが開発し、世界的に有名な生産管理手法「かんばん方式」
「かんばん方式」。それくらい知ってるよ、という人も多いでしょう。
自動車会社のトヨタが作り上げた生産を効率よくする方法だろう? その通りです。
でも、「かんばん方式」という名前は有名でも、具体的にどうやって作業をするのか分からない人も多いでしょう。そこで、今回は、かんばん方式(ジャスト・イン・タイム)についてちょっと紹介してみましょう。
■生産方式の2つの柱、「自働化」と「ジャスト・イン・タイム」
トヨタ自動車の生産方式には、2つの柱があります。「自働化」と「ジャスト・イン・タイム」です。この2つの柱で、同社は効率化を推し進め、高品質でかつ、徹底的にムダを排除する製品作りを達成しました。
「自働化」は、自動の「動」にニンベンが付いて「働」となっているのがポイントです。
生産ラインで異常(機械の異常、品質の異常、ライン・工程の異常)が発生したら、即座に設備が止まり、担当者がそこへ駆けつけます。機械が止まるため、生産ロスを防ぐことができます。
また、不良を監視する人間が不要になるため、ヒトが機械の番人になる必要がなくなります。そこで、作業者や監督する者の時間を節約し、付加価値の高い仕事へ振り向けることができるのです。
そして、異常の原因を徹底的に究明し、再発防止策を考えて対処するため、人材育成にも役立ちます。
■「ジャスト・イン・タイム」とは
もうひとつの「ジャスト・イン・タイム」とは何でしょう。
ジャスト・イン・タイムとは、生産において、各工程に必要なものを、必要なときに、必要な量だけ供給することです。必要な分だけ生産するので、在庫を徹底的に減らし、コストの向上を行う仕組みです。これにより、人的資源や設備、在庫が限られていても、効率的に生産を行うことができます。
トヨタ自動車の創業者、豊田喜一郎が試行錯誤の末に考え出したものです。
「かんばん方式」は、このジャスト・イン・タイムの代表的な要素です。
■「かんばん方式」の実際
では、いよいよ「かんばん方式」の説明に入りましょう。
トヨタ自動車の「かんばん方式」は、「かんばん」と呼ばれる商品管理のカードを使います。
「かんばん」は2種類あります。(1)「仕掛けかんばん」と(2)「引取りかんばん」です。
生産工程での前工程(部品を製造・供給する側)で使うのが(1)の仕掛けかんばん。
後工程(部品を組み立てる側)で使うのが、(2)の引取りかんばんです。
かんばんにはそれぞれ、部品の種類・型番・数量・仕入れ先・納入先・保管場所などのデータが記されています。また、仕掛けかんばんには、その部品を納品するまでの時間なども記されています。
部品置き場には、(1)仕掛けかんばんを付けた部品箱が置かれています。
部品箱には、かんばんに記された通りの型番・数量の部品が入れられています。
【後工程(組み立て側)での動き】
まず、後工程で部品がなくなったとしましょう。すると、(2)の引取りかんばんを持って、後工程の担当者が、部品箱を取りにいきます。
部品箱には(1)の仕掛けかんばんが貼り付けてあります。そこで、部品箱から仕掛けかんばんを外して、(2)引取りかんばんを部品箱に付けて、持って行きます。外した仕掛けかんばんは、部品置き場に掲示しておきます。
引取りかんばんを付けた部品箱は、担当者によって、後工程に運ばれます。
その部品を使う時に、引取りかんばんが外され、後工程に掲示されます。
掲示された引取りかんばんを見たら、担当者は部品置き場を取りに行きます。この繰り返しです。
【前工程(製造・供給する側)での動き】
後工程の担当者に部品が引き取られたら、部品置き場には、(1)の仕掛けかんばんだけが掲示されます。
前工程の担当者は、仕掛けかんばんを見つけたら、持ち帰ってかんばんに記された数量分の部品を製造します。
製造できたら部品置き場に部品を運び、仕掛けかんばんを付けた部品箱に入れて置いておきます。
この繰り返しです。
かんばん方式は、「後工程引取り方式」です。後工程が使った分だけ前工程の製造分を引き取り、その前工程が、さらにその前の工程の製造分を引き取っていくため、無駄のない受注の連鎖を生み、在庫の最小化を実現します。
■かんばん方式のメリットとデメリット
かんばん方式には、ムダが徹底的に削減でき、在庫を最小限に抑えられるメリットがあります。また、スムーズに動き出すと前工程から後工程にスピーディに製品が届けることができるため、生産効率が非常に上がります。また、製造業だけでなくさまざまな業種に応用が利くこともメリットです。
このようにメリットの多い方法ですが、一方でうまく方式が回らないと、欠品が出る可能性が高くなります。また、売上が時期により大きく変動し、生産量の見極めがつきにくい商品や、賞味期限が短い食料品などの製造には不向きです。また、かんばんをつけ忘れたり、紛失するなどの事故も起きやすいデメリットもあります。
かんばん方式は、さまざまな現場で使われたり応用されています。ただ、完全に効率よく運用するには、相応の技術や熟練した人材、よく練られた生産計画が必要です。うわべだけ真似ても、トヨタのような効率のよい生産現場を作り出すのは並大抵ではないといえるでしょう。
しかし、かんばん方式には教えられる点が数多くあります。あなたも自分の会社の生産方式を、かんばん方式を視点に置いて見直してみるのがよいでしょう。